Gilding
Download PDFGilding is an ancient traditional technique, which can be done on wood, metal, glass, ceramic, stone or marble, to cover an object with gold. By extension, we use « gilding » when it is an application of copper or any other metal imitating gold.
Known since Antiquity, especially in Ancient Egypt, gilding was used at all times and in all parts of the globe.
In France, Louis XIV used this precious metal, especially during the colossal construction of the Palace of Versailles: furniture, paneling, railings, fountains and roofs were covered with gold leaves.
There are several different gilding techniques depending on the type of support (metal, wood, glass or stone).
1 – Gilding on wood
Largely used especially for the realization of gilt wood overmantel pierglass, gilding on wood requires a special preparation of the support called preparation of primers.
In fact, wood is an organic material, consequently its reaction depends on hygroscopic variations (the wood fiber swells and shrinks as a function of the quantity of water in the air).
It is therefore essential to prepare the surface of the wood before placing the gold leaves. A coating made of finely ground chalk, a binder (sheep skin glue or, since the 16th century, rabbit skin glue) and a solvent (water) was therefore elaborated since the Middle Ages and named "primer". This primer is applied at 60 ° C in 10 to 12 layers, then the surface is smoothed and covered with two layers of Armenian bole at the surfaces that will be burnished (it is a kaolinic clay of red color used to fix the gold, also called Bolus Armenus or Armenian bole). This substance is a soft bottom that provides a bright and very smooth gold through burnishing. In addition, it gives gold red reflections by transparency.
Once the primers are finalized, we can make the gilding.
The water gilding is to apply the gold leaves with water on the Armenian bole. The matting of the gold will be obtained by covering the gold leaves with a light layer of skin glue: the gold thus becomes mat. The brilliances of gold will then be obtained thanks to the burnishing, that is to say the crushing of the agate stone.
Until the end of the 18th century, water gilding was the only one known for all the objects in wood.
From the 19th century, wood can also be gilded thanks to the gilding paste (linseed oil) which is easier than water gilding. However, gilding paste will not be able to have the same dull and shiny contrasts as a water gilding.
2 – Gilding on metals
A metal support (copper, brass or bronze) can be gilded in particular thanks to four processes:
Fire-gilding (also known as Mercury-gilding or Wash-gilding) is a mixture of mercury and molten gold. Mercury, the only metal with liquid form at room temperature, has the property of dissolving gold. The amalgam created by mercury and gold is applied on the object made of perfectly sanded metal which is then heated in the oven or with a blowtorch. Thanks to the heat, the mercury will evaporate completely (if it is not completely evaporated, it forms whitish spots). Finishing stage can be done by burnishing or scratch-brushing.
« Make scratch-brushing on an object, it is to make disappear the mat which covers it, or simply to clean its surface by the active and prolonged friction of a set of stiff and straight set of wires points. The instrument we use is called scratch-brush; its shape varies according to the objects. " (Guide pratique du doreur, de l’argenteur et du galvanoplaste par Alfred Roseleur, Paris 1873).
Burnishing consists of crushing the gold layer on the support using a tool called burnisher which is a hard and hafted stone often made of agate. This process gives a very beautiful gilding, very solid and lasting, applied only on small objects which often are bronzes and sculptures especially since the Renaissance.
Largely used by Louis XIV for the Palace of Versailles , fire-gilding is today almost abandoned because of the high toxicity of the process that caused the rapid death of craftsmen.
The Demidoff Vase, made in 1819 by the sculptor and bronzemaker Pierre-Philippe Thomire in malachite veneer and gilt ormolu, is a superb example of fire-gilding. This vase, almost two meters high, was ordered by Count Nicolas Demidoff to furnish Villa San Donato, his residence near Florence, Italy. The vase is now preserved at the Metropolitan Museum of Art in New York.
Electroplating is known since Antiquity but was industrialized in the middle of the 19th century especially by Charles Christofle and dethroned fire-gilding.
This high quality process is more economical ; thanks to it, some thin layers of gold are deposited. This type of gilding consists in depositing a fine gold inlay on a metal surface (silver, copper, brass ...) thanks to the electrolytic process. Electrolysis is made in large tanks containing water and metal salts.
This process uses Liugi Galvani's discovery: it consists in plunge two metal electrodes into a large tank containing a bath of water and metal salts, forming an electric cell. Power in the two electrodes causes displacement of metal molecules from one electrode to the other, from the anode to the cathode; this is called galvanizing.
Using this method and the electric cell discovered by Volta, the Italian physicist Luigi Valentino Brugnatelli succeeded in 1805 in depositing gold on silver objects immersed in a solution of gold chloride.
In 1837, the Russian physicist Boris Jacobi of Saint Petersburg publishes the process and it is from that time that it is really known, thanks to the realization of the sculptural decor in the Saint Isaac's Cathedral in Saint Petersburg, Russia, entirely made of electroplating (circa 1840-1850).
At the same time, the English Henry and Georges-Richard Elkington registers a patent on September 27, 1840. The same year, on December 19 the French Henri de Ruolz-Montchal does the same, and they do not know each other.
In 1842, Charles Christofle, in Paris, begins to exploit their patents and develops the technique of electroplating on objects. In 1845, he founds the company "Charles Christofle and Cie" which will have a great success. He begins making his own pieces in 1846 and becomes completely independent and mastering the technique of electroplating to perfection.
Gilding paste is another technique of gilding on metal, which can be applied to large objects (domes, railings ...), which is difficult to achieve with the two previous techniques. The support is first cleaned and polished in order to have a surface like a mirror. The gold is then presented in its form of leaves stuck by the paste (linseed oil at 150 ° C with a metal salt). The whole is finally varnished. This gilding is considered fragile and not resistant to scratching, so the technique is usually reserved for architectural elements that can’t receive shocks.
Finally, there is an other technique for gilding metals : the gilding with varnish. Actually this method does not use gold at all but a yellow varnish applied on heated brass. Generally, only copper and its yellow alloys are varnished. It is a gilding that is commonly used, especially since Louis XIV who made the recommendation to save gold. The gilding with varnish is not a lasting method: it crackles and the metal oxidizes.
3 – The gilding on glass and on ceramics
For this type of object, fusion gilding is the most commonly used method. Once the gold leaf is placed on the glass or ceramic, the object is heated to a high temperature so that the gold permanently adheres to the support.
For the glasses, we can also use a technique of gilding paste known since the Antiquity but developed in Bohemia from the 17th to the 19th centuries and called "Zwischengoldglas", which means "Gold between glasses". These are two-part glasses that fit into each other. The inner glass is adorned with gold leaf on its outer part. The leaf is then engraved with the stylets. This first glass is then inserted in the second glass, slightly larger and the whole is welded.
4 - Gilding on stone and marble
Gilding on stone and marble has been used since Antiquity, in Greece and Egypt, where it was used to decorate religious edificis and sculptures.
The support is porous, so it should be insulated with a varnish. Then the gold is applied in leaves, glued with paste.
Bibliography :
La Revue Experts n° 01 – 03/1988
Gilles Perrault, Dorure et polychromie sur bois - Techniques traditionnelles et modernes, éditions Faton, Dijon, 1992, 190 p.
M. J. Saulo, La dorure sur bois, éditions Roret, coll. « Manuels Roret », Paris, 1886. — Réédition en fac-similé : Nouveau manuel complet de la dorure sur bois à l'eau et à la mixtion par les procédés anciens et nouveaux ; suivi de : La Fabrication des peintures laquées sur meubles et sièges, édition L. Laget, Paris, 1977, XII-164 p
Alfred Roseleur, Guide pratique du doreur, de l'argenteur, et du galvanoplaste, Éditeur de Plazanet, Paris, 1873
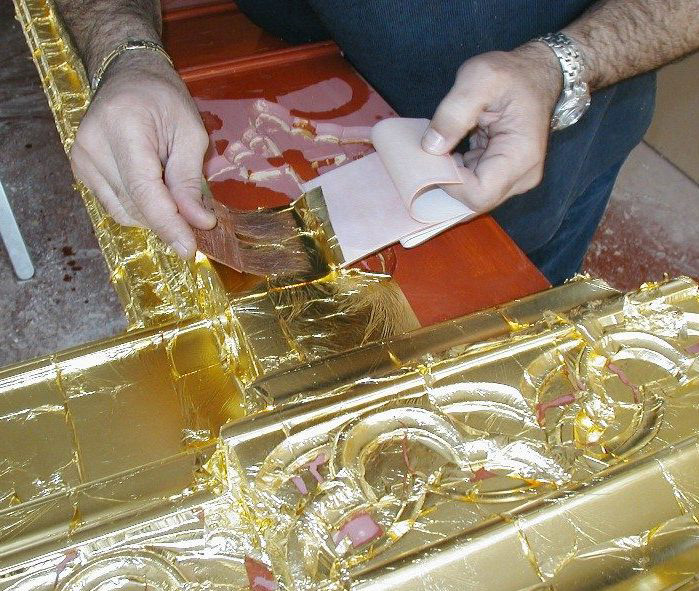
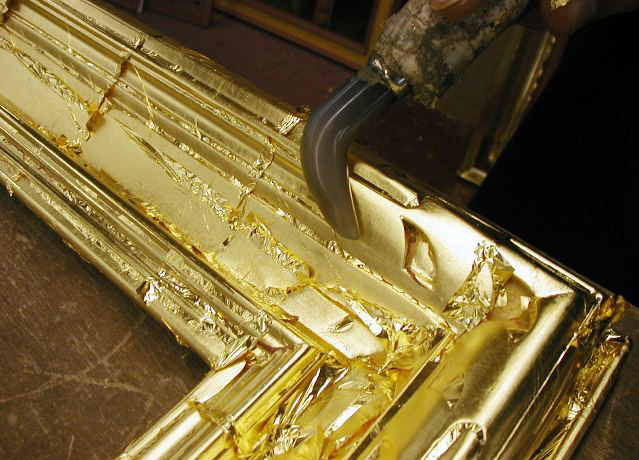
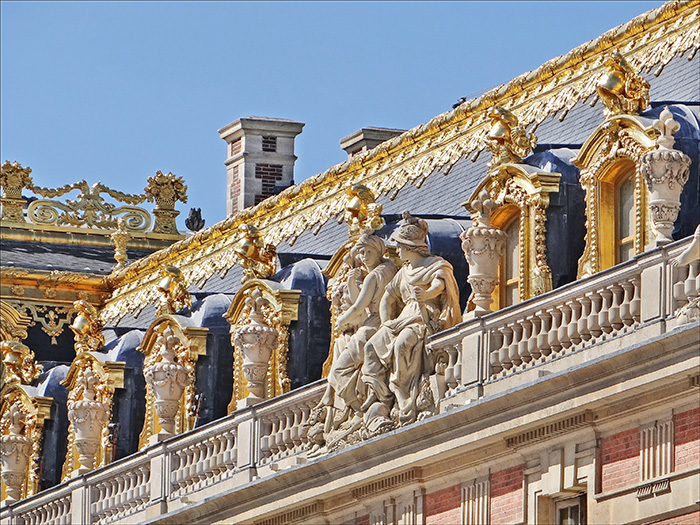
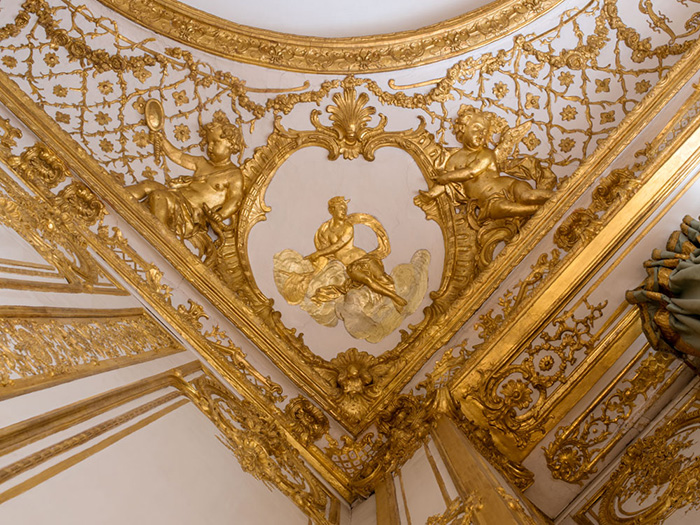
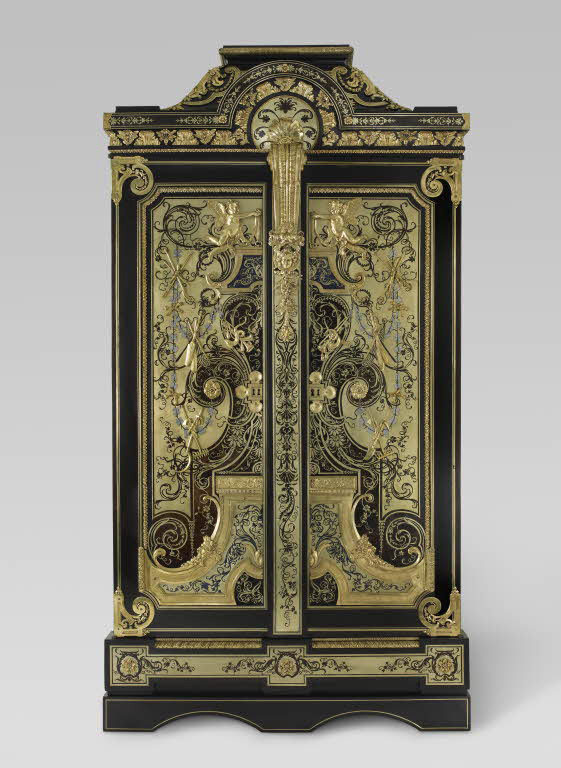

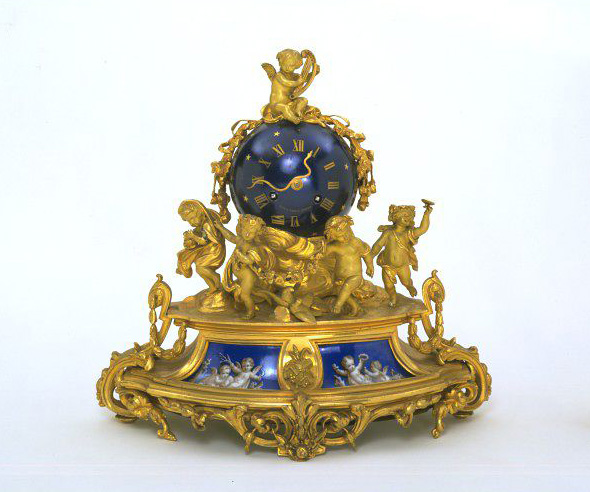
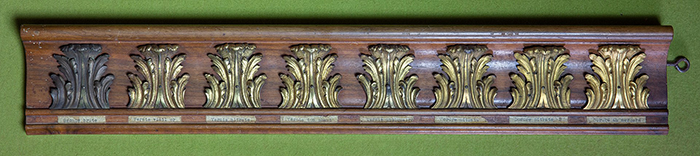
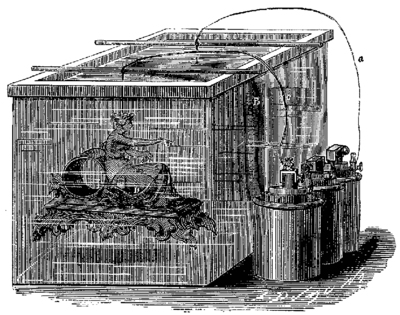
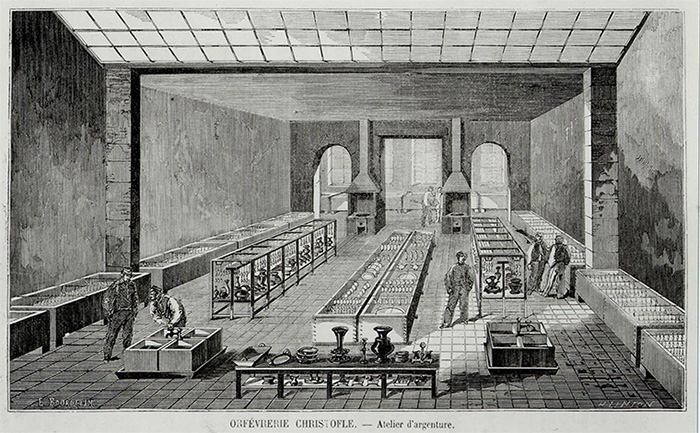
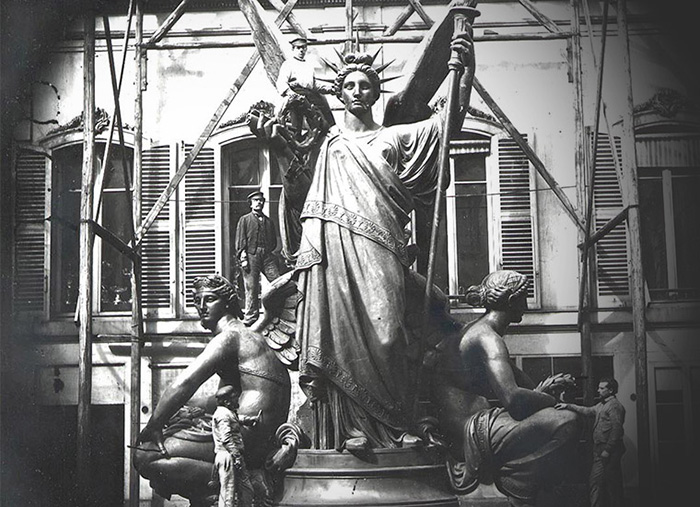
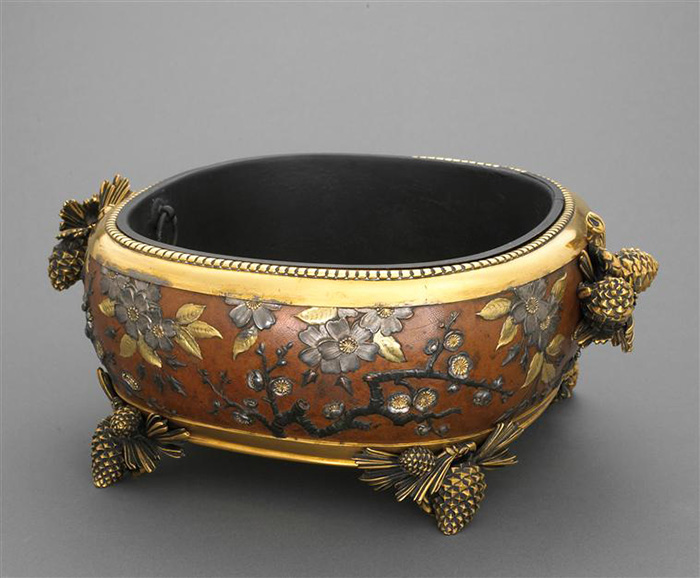
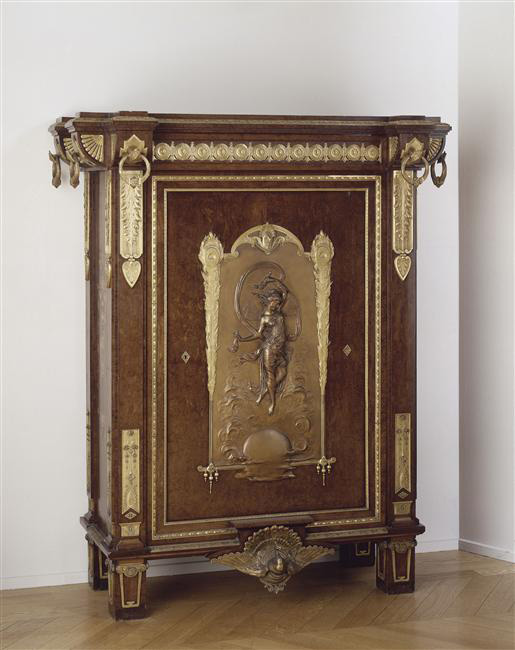
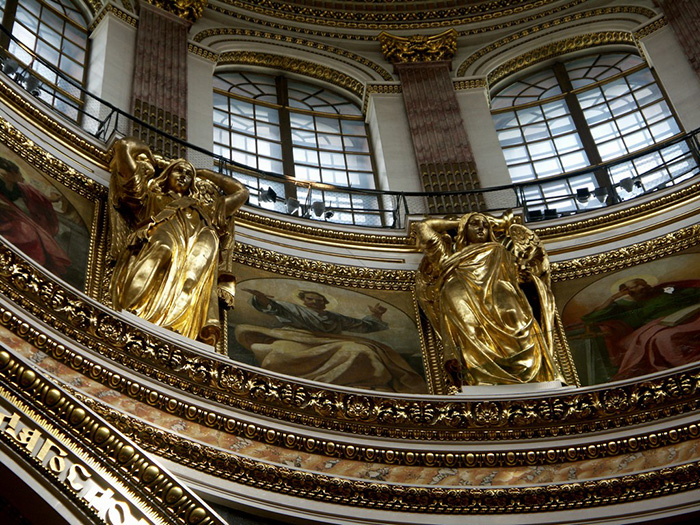
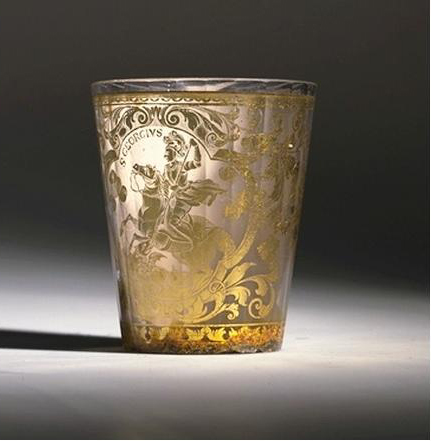
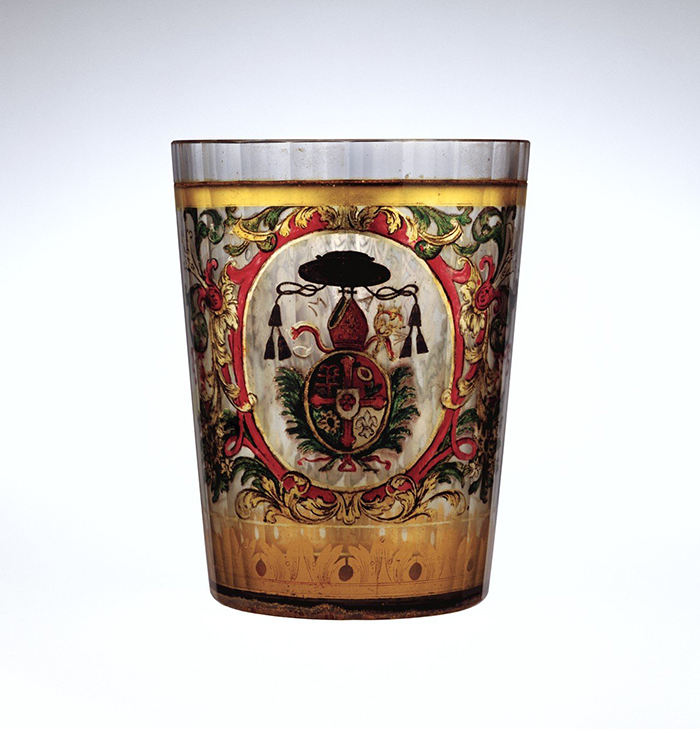